Acfri, le spécialiste français de la cellule de refroidissement, vient de terminer l’immense chantier de modernisation de son unité de production située à Bondoufle (91).
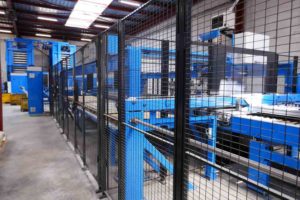
La PME française
Acfri est désormais armée pour répondre à tous les besoins des professionnels de la restauration en matière de refroidissement de denrées ! Initié fin 2017, un chantier de près de 5 millions d’€ a permis à cette entreprise familiale d’agrandir l’unité de production de Bondoufle basée en Essonne (91). Après avoir acquis le terrain mitoyen, l’expert mono-produit a agrandi l‘usine de près de 1000 m
2 pour installer une ligne de panneautage ultra moderne qui lui permet de sélectionner les plaques d’inox qui structurent les cellules, de les poinçonner et de les plier automatiquement. «
Cet investissement de près de 2 M d’€ nous a apporté une énorme flexibilité et un gain en terme de précision. En outre, la ligne a permis de supprimer les tâches fastidieuses génératrices de TMS (ndlr : Trouble Musculo Squelettique) » explique
Sébastien Comby le directeur Général. Les équipes qui réalisaient ces tâches jusque là ont été replacées sur des postes à plus forte valeur ajoutée (contrôle qualité, logistique etc.). La réorganisation de cette zone de production a été directement supervisée par
Richard Comby, Président d’Acfri mais également ingénieur de formation. C’est lui qui développe toutes les nouvelles solutions techniques de l’entreprise.
1000 autre m
2 ont été réservés au stockage, une surface qui permet d’avoir désormais sur plus de 20 références courantes, un stock de cellules toujours prêtes à être expédiées.
Le refroidissement rapide plus que jamais d’actualité
L’anticipation de cet investissement auquel s’est ajouté une rénovation complète des locaux administratifs et la création d’une salle de R&D connectée, l’Acfri LAB, tombe à pic ! En effet, avec les nouveaux impératifs environnementaux (F-gas en particulier), le fabricant a été obligé de s’adapter aux nouveaux standards de conception. En partenariat avec les principaux acteurs du marché, l’entreprise a mis en place une étude technique et opérationnelle de compatibilité de ses équipements avec l’ensemble de l’offre fluide et groupes frigorifiques du marché. Ainsi, dès à présent, le fabricant est en mesure de proposer une gamme de cellule compatible C0
2 avec deux niveaux de pression de service, 45 et 80 bars. En complément, grâce aux tests qui sont actuellement réalisés en configuration réelle de fonctionnement dans l’Acfri LAB, l’entreprise s’est fixée comme objectif d’être le premier fabricant français à proposer une gamme de cellule très basse température qui sera compatible avec les fluides GWP 150 de nouvelle génération. Ses offres actuelles peuvent être éligibles aux certificats CEE, une opportunité pour les utilisateurs qui, par ce biais, bénéficient d’une baisse importante de leurs consommations énergétiques et d’un accompagnement financier de leur investissement.
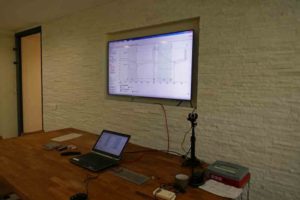
Autre dossier sur lequel Acfri s’investit : le refroidissement des barquettes en cellulose qui se généralisent en restauration collective et qui nécessitent un refroidissement spécifique du fait de leur haut pouvoir isolant, supérieur aux habituelles barquettes en plastique.
«
L’Acfri Lab est un espace polyvalent où il est possible de tester tous les process. En matière de refroidissement, notre expérience nous a montré qu’il n’y a pas de standard et nous invitons les professionnels à anticiper leurs besoins en venant les tester chez nous pour trouver la meilleure solution » commente Sébastien Comby. L’Acfri LAB permet également d’organiser des visioconférences et des formations avec notamment le logiciel Acfri Soft de traçabilité. «
C’est devenu indispensable avec nos clients français mais aussi pour ceux qui sont à l’étranger ». Acfri réalise 15% de son chiffre d’affaires (10 millions d’€) à l’Export, un chiffre qui devrait doubler dans les 3 ans puisqu’il est actuellement en progression constante. Il faut dire que la PME multiplie les succès à l’étranger comme, dernièrement, en Afrique du Sud où elle vient d’équiper l’usine In2Food de Johannesburg avec des tunnels de refroidissement 100% Made in France !